CERN Water Distribution
CERN Demineralised Water Distribution Network general data can be illustrated by a table like the following one. More detailled
features here
.pdf or here
.pdf
LHC Water Layout Characteristics
- Solders are forbidden inside an electrical power module: water pipe must be made on one piece (water plate for example).
- Water flow is passively obtained with regards to the natural water pressure drop of the converter: no "active" device.
A major part of all design calculation described below are extracted from a document from Davide Tommasini (CERN).
Power Converter, and more specifically Rack and Power Module (s) distribution has to fit several general rules:
- In cases of Rack interal parallel paths, they must be individually controlled and interlocked.
- Rack Water distribution pressure drop must be kept as minimum as possible, with water pressure drop normally contained in Power Modules.This point is absolutely critical in case of a rack distribution filling two rack internal paths in parallel, to ensure a good water flow sharing. All Rack common path will then be designed adequately, since driving the full flow-rate, ant then leading naturally to worst conditions for pressure drop.
- Quick-Fit Coupling are a critical point regarding reliability. Water pressure drop of these devices are generally low. See example on 1/4" solution being measured .png.
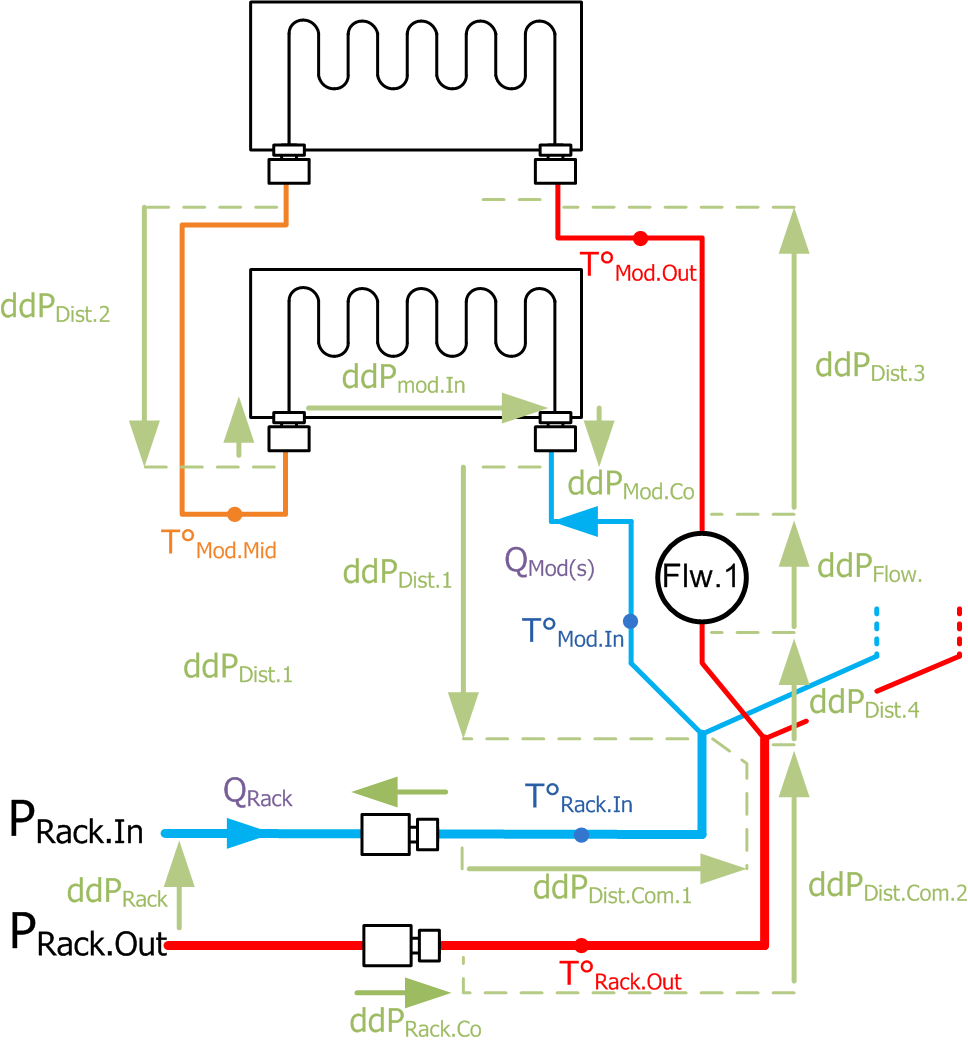
Example of a Rack Internal distribution: 2 paths - 2 Modules in series .vsd
We generally use these conventions:
- Rack General Water Layout Input & Output: flexible hoses terminated by Female water Connector for both.
Goal is to protect rack water connectors (transport), female connector assumed to be less fragile.
- Power Module Water Layout Input & Output: Male water Connectors for both.
Male connectors on removable power module so that flexible hose attached to the rack are then also terminated by female connector.
Coupling connexion is assumed to be more handy when plugging the female part in a "static" male part.
- Input Connector/Connexion = Blue
Water leaving the module is generally hotter than when entering it (cold=blue).
- Output Connector/Connexion = Red
Water leaving the module is generally hotter (red=hot) than when entering it.
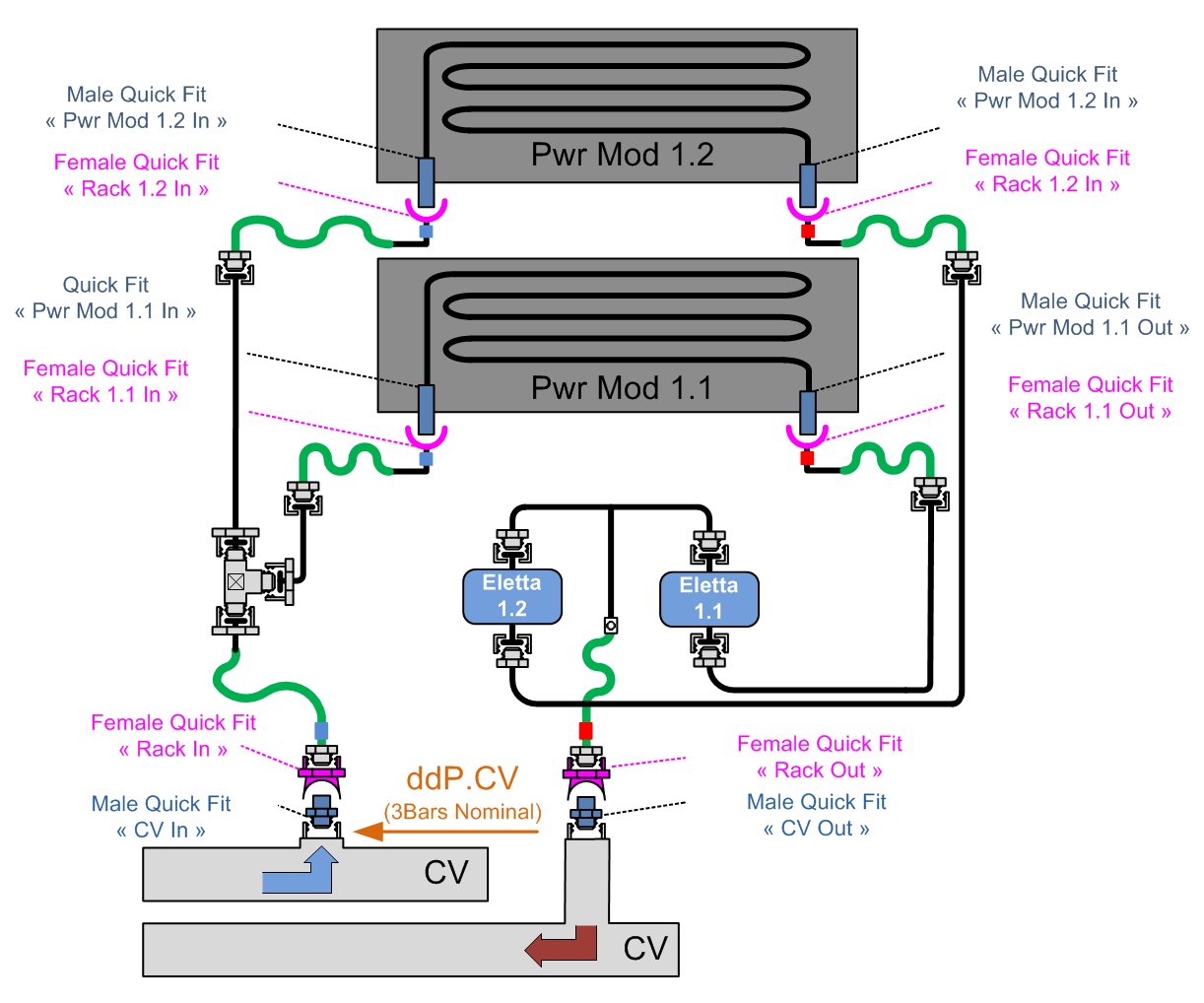
Example of a M/F convention application and a Power Module realization example
Water cables generally doesn't tolerate high mechanical stress, or high bending curves:
Example of a Parker cable being damaged after 4 years of use under too high stress (curvature) conditions
Thermal design must always be compatible with water network installed, and especially its regulation mode. A general water layout controlling the delta.temperature is completly different from a delta.pressure one, especially when collecting several different equipements.
Water flow requirements:
Energy transfer in water uses the well-known formula:
E=m.C.dT (E=Energie [J], m=weight [kg], C=chaleur massique [J/(°C.kg)], dT=Temperature difference [°C])
This formula applied to a flowrate gives the following formula:
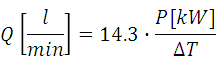
Formula-1: Water Flow vs Power vehiculated in water & its temperature rise
Designing a thermally effective transfer:
To be thermally effective, the water flow shall be moderately turbulent; this condition is met if the so called Reynolds number R
e, representing the ratio between the inertial forces and the viscous forces, is greater than 2000 and smaller than 10E5. Calculation of the Reynolds number is given by the formula:
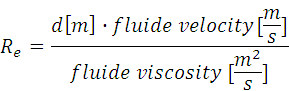
Formula-2: Reynolds number calculation
Formula which required the calculation of the fluide velocity

Formula-3: fluide velocity calculation
Leading then to the simplified formula (water @ 40°C) for the calculation Reynolds

Formula-4: Reynolds number simplified calculation with 35°C water dynamic viscosity : 0,7.10E-4 Pa.s, and then a fluid viscosity of 7E-7 m²/s
Leading finally to the very handy formula (water @ 40°C) for achieving a efficient thermal cooling
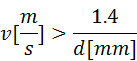
Formula-5: Efficient cooling conditions (water @ 40°C)
On the other hand, excessive water speed my cause erosion corrosion of the cooling pipe: in copper this starts taking place at velocity > 3m/s. This is one of the reasons why efficient cooling in small pipes always produces some erosion.
To find the good combination of diameter and water velocity for a given flow this condition shall be iterated with:

Formula-6: Efficient cooling conditions (water @ 40°C)
Calculation of the pressure drop:
A very important parameter is the pressure drop of a water layout, for matching the water network. Some web pages exist (
here). For hydraulically smooth pipes of length L and diameter d with inlet as outlet at about the same height, with moderately turbulent flow, the pressure drop is given by the Blasius law which, in practical units, can be written as:
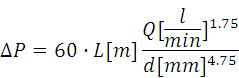
Formula-7: Estimation of a given layout water pressure drop
Validation of reliable design
Another very important parameter is the power level being transmitted through / in water Above a certain level, cavitation will appear, destroying locally the material (whatever it is).
P.transmitted < 8 Watts / cm2
(above 50 Watts / cm2, the conditions are very challenging and would likely lead to material destruction).
Water cooled converters shall be designed and tested following the "regles de l'art" (PED Article 4 paragraph 3. $2.c.ii not applicable PSxDN < 5000).
For type tests, the pressure inside the cooling system of a liquid cooled PECS (see IEC62477-1 $4.7.2.3.3) shall be increased at a gradual rate until a pressure relief mechanism (if provided) operates, or until a pressure of twice the operating value or 1,5 times the maximum pressure rating of the system is achieved, whichever is the greater.
For the purpose of this test the coolant pump may be disabled.
For routine tests, the pressure shall be increased to the maximum pressure rating of the system. The pressure shall be maintained for at least one minute. There shall be no thermal, shock, or other hazard resulting from the test. There shall be no leakage of coolant or loss of pressure during the test, other than from a pressure relief mechanism during a type test.
For both type and routine test, the pressure shall be maintained for at least one minute.There shall be no thermal, shock, or other hazard resulting from the test. There shall be no leakage of coolant or loss of pressure during the test.
At CERN, HSE requires 1.43x maximum pressure (16 bars) = 22.9 bars.
LPC water cooled converters shall respect:
- A type test with pressure increasing at a gradual rate until a pressure of 24 bars is achieved and maintained for at least one minute;
- Routine tests, with pressure increased up to 24 bars and maintained for at least one minute.
Important note: if an Eletta is present in the circuit, specific conditions should be applied with individual items tested at 24 bars except Eletta, and final circuit tested up to 16 Bars.
Water Cooled Plate design
Water cooled plates can based on a sandwitch design, giving high flexibility for power design and component placement.
Water Cooled Plate Example and Assembly principles .vsd
Some formulas can be used to better caracterize the thermal environment.
Formula-9: Thermal resistance of a given material & case of pipe. (longueur L, diameter external & internal, thermal conductivity)